Galvanized Steel Pipe Polishing Features
In order to prolong the service life of pipelines, pipeline anti-corrosion construction has become an indispensable process in the pipeline production process; with the continuous development and production of manufacturers, various types of anti-corrosion spiral steel pipes have appeared on the market.
The more common anti-corrosion types of spiral steel pipes on the market are: epoxy resin anti-corrosion, 3PE anti-corrosion, cement mortar anti-corrosion and epoxy asphalt anti-corrosion; different types of anti-corrosion steel pipes have different uses, and spiral welded steel pipes refer to those with seams on the surface. Steel pipes, which are welded with steel plates or steel plates to form round or square shapes;
Spiral steel pipe factory can be divided into arc welded pipe, high frequency resistance welded pipe, low frequency resistance welded pipe, gas welded pipe, furnace welded pipe, etc. according to different welding methods; according to the shape of the weld, it can be divided into straight seam welded pipe and spiral steel pipe, electric welded steel pipe for oil Drilling and machinery manufacturing; furnace welded pipes can be used as water gas pipes, large-diameter longitudinal welded pipes are used for high-pressure oil and gas transportation, spiral steel pipes are used for oil and gas transportation, pipe piles, bridge piers, etc.; compared with seamless steel pipes, welded steel pipes have lower cost and production higher efficiency.
Drinking water anti-corrosion steel pipe topcoat: It is composed of epoxy resin, rubber resin modification, harmless anti-rust pigments, fillers and additives, and has excellent chemical resistance and anti-microbial erosion.
Uses: It is used as primer for water supply pipelines, and topcoat is used for anti-corrosion coating on the inner wall of water supply pipelines; this kind of anti-corrosion is for drinking water pipeline projects, and it is non-polluting and harmless.
Maintenance measures:
1. The product should be stored in a cool, ventilated, dry place, away from fire and heat sources.
2. This product is a thick coat and can be applied in thick coats without sagging. Generally, after opening the barrel, it can be used without adding thinner.
3. After the paint is stored for a long time, there will be slight precipitation, so it should be stirred before use.
4. After the paint is ready, it should be cured for 20 minutes in summer and 1.5-2 hours in winter for construction. Usually use up within 8 hours, otherwise the viscosity will thicken and the application will not be easy.
5. The top coat can be applied after the primer surface is dry. This interval should not exceed two days at room temperature, otherwise the adhesion between the layers will be affected. The time interval between top coats should also allow the surface to dry. Interpenetrating network polymer is a new type of IPN series anti-corrosion coating researched and developed in the past twenty years. It is a copolymer of castor oil-based polyurethane and polysubstituted ethylene interpenetrating network polymer. During the mixing and curing process of paint, the former is rubber, and the latter’s plastic network penetrates into each other, penetrates and firmly adheres to the surface of the object to be coated, thus producing corrosion protection and decorative materials on the surface of the paint.
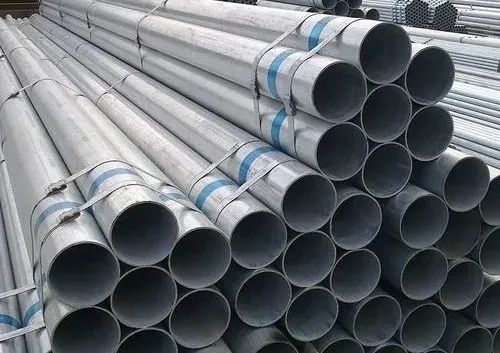
Leave a Reply
Want to join the discussion?Feel free to contribute!