Inspection Standards for FBE Anticorrosive Coatings
FBE (Fusion-Bonded Epoxy) anticorrosive coating inspection standards encompass international, national, and industry specifications, focusing primarily on coating performance parameters and acceptance requirements. Below is a detailed overview of the core standard systems and key technical indicators:
I. International Standard System
- ISO 21809 Series
- ISO 21809-1:2018: Specifies that the FBE primer layer thickness in 3-layer polyethylene (3LPE)/polypropylene (3LPP) coatings shall be ≥300μm, with adhesion ≥5MPa.
- ISO 21809-11:2019: Requires field joint and repair coatings to match the original coating thickness and pass the cathodic disbondment test (65°C, 28 days) with a disbondment distance ≤10mm .
- ISO 12944-6: Salt spray testing (ISO 9227) mandates that FBE coatings withstand 1,000 hours of testing without blistering or rusting .
- ASTM Standards
- ASTM D4541-22: Adhesion testing requires a pull-off strength ≥5MPa and a loading rate of 0.8MPa/s ±10% .
- ASTM G42-11: High-temperature cathodic disbondment testing (80°C, 0.5MPa) allows a maximum disbondment distance of ≤15mm .
- ASTM A 775/A 775M: General standard for epoxy coatings, specifying requirements for coating thickness, adhesion, and continuity.
- NACE SP0169-2024
- Coating insulation resistance ≥10,000Ω·m², with a cathodic protection potential ≤-0.85V (vs CSE) .
II. Chinese National Standards
- GB/T 39636-2020 (Core Standard)
- Épaisseur: Single-layer FBE: 350μm ±50μm; double-layer FBE: total thickness ≥600μm, with local minimum thickness ≥80% of the design value.
- Adhesion: Pull-off strength ≥5MPa; cross-cut method grade ≥2 (GB/T 9286-2021) .
- Cathodic Disbondment: Disbondment distance ≤15mm after testing at 65°C for 28 days .
- GB/T 4956-2003
- Thickness measurement accuracy for magnetic substrates: ±10μm, with at least 3 measurements per square meter .
- GB/T 5210-2006
- Pull-off test requires a specimen diameter of 20mm ±0.5mm and surface preparation to Sa2.5 grade.
III. Industry Standards
- SY/T 4113.11-2023 (Replacing SY/T 0063-1999)
- Holiday Detection: High-voltage spark testing voltage calculated as V = 7900\sqrt{T} (T = thickness in mm), with a typical value of 2.1kV (0.4mm thickness) and a holiday density ≤2 defects/m² .
- Low-Voltage Detection: DC voltage ≤100V, used to detect thickness deficiencies .
- SY/T 0315-97
- Double-layer FBE total thickness ≥600μm, requiring passage of a 1.5J impact test and 3° bend test without disbondment .
- SY/T 7036-2016
- Compatibility requirements for coatings and cathodic protection in oil and gas station pipelines: current density ≤10μA/cm² .
IV. Special Scenario Standard Requirements
- High-Temperature Environments
- Hot oil pipelines must pass the ASTM G42 test (80°C, 0.5MPa) with a disbondment distance ≤15mm .
- Glass transition temperature (Tg) must exceed 80°C, verified via DSC testing.
- Buried Pipelines
- Coating insulation resistance ≥10,000Ω·m², with a cathodic protection potential ≤-0.85V (vs CSE).
- Combined with Close Interval Potential Survey (CIPS) to assess defect distribution.
- Repair Projects
- Repaired areas must meet thickness, adhesion, and holiday detection requirements, with interface bond strength ≥4MPa.
V. Surface Preparation and Calibration Specifications
- Surface Preparation Standards
- Sandblasting cleanliness grade must reach Sa2.5 (GB/T 8923.1) or SSPC-SP 10 (near-white grade).
- Equipment Calibration
- Thickness Gauges: Calibrated using standard test blocks (e.g., 350μm ±5μm), with an error ≤±5%.
- Spark Testers: Verified daily using calibration plates with artificial defects, ensuring voltage error ≤±2%.
- Reporting Requirements
- Test data must include location, equipment model, calibration records, and bear CMA/CNAS accreditation stamps.
Through this standard system, the thickness, adhesion, corrosion resistance, and compatibility with cathodic protection of FBE anticorrosive coatings can be comprehensively evaluated, ensuring long-term reliability in oil & gas, chemical, and other industrial applications.
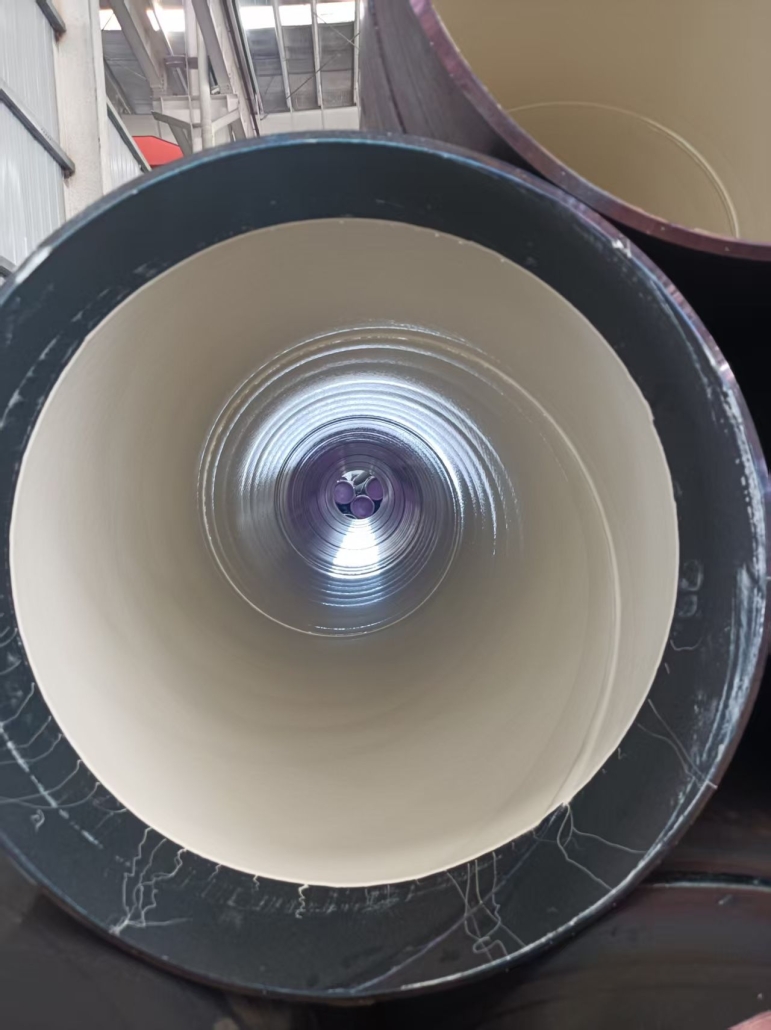