Hot-dip Galvanized Steel Pipe Welding Construction Process
Before hot-dip galvanized steel pipe welding, the hot-dip galvanized steel pipe is mainly heated, and welding begins after temperature control for 30 minutes. The heating, solid layer temperature and heat treatment process of welding are automatically controlled by the temperature control cabinet of the heat treatment process. The far-infrared crawler heat treatment furnace is used to automatically set the curve and describe the curve, and the thermal resistor measures the temperature.
During heating, the distance between the thermal resistance measurement points is 15mm-20mm from the weld boundary. In order to better prevent the hot-dip galvanized steel pipe from welding deformation, each column joint is welded symmetrically by two people, and the welding direction is from the middle to both sides.
When welding the inner opening, the first to the third layer must be operated in small specifications, because its welding is the primary cause of welding deformation.
After welding one to three layers, clean the reverse side. After removing the root with carbon arc air gouging, the weld needs to be mechanically polished and polished, and the weld surface needs to be combed for nitriding treatment to expose the metal texture to prevent the surface from being optimistically carbonized and cracked. The outer mouth needs to be welded once, and there will be some residual material in the inner mouth. When welding the second layer of hot-dip galvanized steel pipe, the welding direction should be opposite to that of the layer, and so on. Each layer of welding joints should be spaced 15-20mm apart.
When welding hot-dip galvanized steel pipes, the welding current, welding speed and number of welding stacks of the two welders should be consistent. When welding, the welding should start from the arc starting plate and end on the arc starting end plate. Cut off and grind and polish after welding.
Post-weld heat treatment: The heat treatment process should be carried out within 12 hours after the weld is welded. If the heat treatment process cannot be carried out immediately, insulation, slow cooling and other methods should be used. After the quenching and tempering treatment is completed, two thermal resistors should be used to measure the temperature, and the thermal resistors should be welded on both sides of the weld. According to the “Standards for Construction and Inspection of Steel Structure Engineering”, the welds are inspected by ultrasonic flaw detectors, and the inspection market share is 100%.
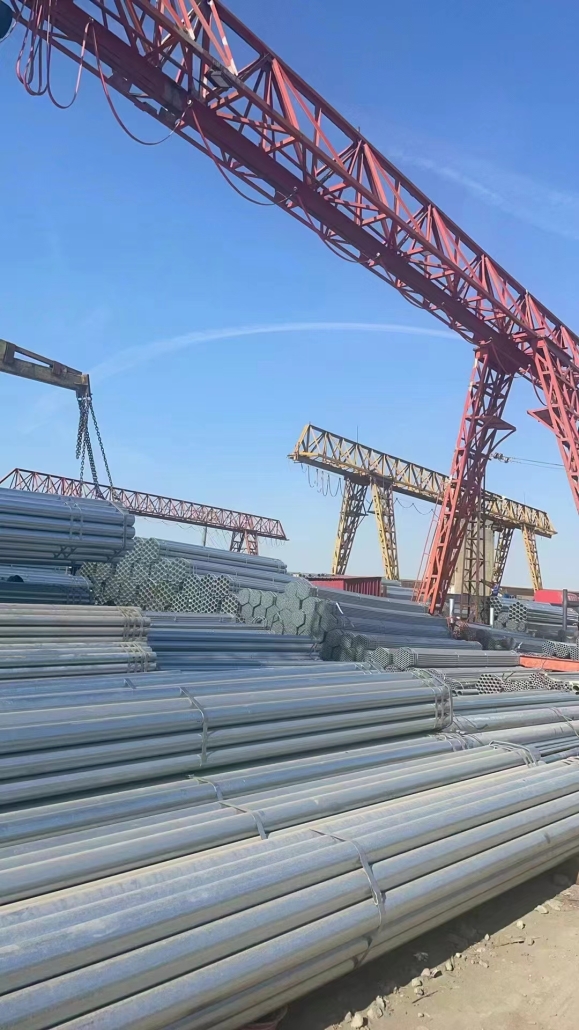
Dejar un comentario
¿Quieres unirte a la conversación?Siéntete libre de contribuir!