Formgebungsverfahren für geschweißte Stahlrohre mit gerader Naht
Hinsichtlich der Schweißtechnik lassen sich nahtlose Stahlrohre in widerstandsgeschweißte nahtlose Stahlrohre und unterpulvergeschweißte nahtlose Stahlrohre unterteilen. Widerstandsgeschweißte nahtlose Stahlrohre werden weiter unterteilt in hochfrequenzgeschweißte nahtlose Stahlrohre, mittelfrequenzgeschweißte nahtlose Stahlrohre und niederfrequenzgeschweißte nahtlose Stahlrohre. Unterpulvergeschweißte Stahlrohre mit gerader Naht werden auch als doppelseitig unterpulvergeschweißte Stahlrohre mit gerader Naht oder LSAW-Stahlrohre mit gerader Naht bezeichnet, wobei LSAW die Abkürzung für Longitudinally Submerged Arc Welding ist.
Elektrisch widerstandsgeschweißtes Stahlrohr mit gerader Naht wird auch als ERW-Stahlrohr mit gerader Naht bezeichnet. ERW ist (Electric Resistance Weldin), und die Abkürzung ist ERW. Hochfrequenzgeschweißtes geradliniges Stahlrohr wird auch als ERW-geradliniges Stahlrohr bezeichnet. ERW ist ein allgemeiner Begriff für widerstandsgeschweißte Stahlrohre. Hochfrequenz-Widerstandsschweißgerade (Electric Resistance Welding, kurz ERW) ERW ist der erste Buchstabe des entsprechenden englischen Wortes.
Widerstandsgeschweißte Stahlrohre werden in zwei Formen unterteilt: AC-geschweißte Stahlrohre und DC-geschweißte Stahlrohre. Das Wechselstromschweißen wird je nach Frequenz in Niederfrequenzschweißen, Mittelfrequenzschweißen, Supermittelfrequenzschweißen und Hochfrequenzschweißen unterteilt. Das Hochfrequenzschweißen wird hauptsächlich für die Herstellung von dünnwandigen Stahlrohren oder normalwandigen Stahlrohren verwendet. Das Hochfrequenzschweißen wird in Kontaktschweißen und Induktionsschweißen unterteilt. Das Gleichstromschweißen wird im Allgemeinen für Stahlrohre mit kleinem Durchmesser verwendet.
Die wichtigsten Schritte sind wie folgt:
1. Erkennung von Blechen: Nachdem die Stahlbleche, die für die Herstellung von unterpulvergeschweißten geraden Stahlrohren mit großem Durchmesser verwendet werden, in die Produktionslinie gelangen, werden sie zunächst einer Ganzblech-Ultraschallprüfung unterzogen;
2. Kantenfräsen: Verwenden Sie eine Kantenfräsmaschine, um beide Kanten des Stahlblechs beidseitig zu fräsen, um die erforderliche Blechbreite, Parallelität der Blechkanten und Fasenform zu erreichen;
3. Kante vorbiegen: Verwenden Sie eine Vorbiegemaschine, um die Kante der Platte so vorzubiegen, dass die Kante der Platte eine Krümmung aufweist, die den Anforderungen entspricht;
4. Umformung: Auf der JCO-Formungsmaschine wird die erste Hälfte des vorgebogenen Stahlblechs in mehreren Schritten in eine "J"-Form gestanzt, dann wird die andere Hälfte des Stahlblechs in ähnlicher Weise in eine "C"-Form gebogen, und schließlich wird die Öffnung geformt. "O"-Form
5. Vorschweißen: Verbinden Sie die geformten, geradnahtgeschweißten Stahlrohre und verwenden Sie Schutzgasschweißen (MAG) für kontinuierliches Schweißen;
6. Innenschweißen: Verwenden Sie das Mehrdraht-Unterpulverschweißen in Längsrichtung (bis zu vier Drähte), um die Innenseite des Stahlrohrs mit geradem Falz zu schweißen;
7. Außenschweißen: Tandem-Mehrdraht-Unterpulverschweißen wird verwendet, um die Außenseite des längs unterpulvergeschweißten Stahlrohrs zu schweißen;
8. Ultraschallprüfung I: 100% Prüfung der inneren und äußeren Schweißnähte des geradnahtgeschweißten Stahlrohrs und des Grundwerkstoffs auf beiden Seiten der Schweißnaht;
9. Röntgeninspektion I: 100% Röntgen-Industriefernsehinspektion von inneren und äußeren Schweißnähten, mit einem Bildverarbeitungssystem, das die Empfindlichkeit der Fehlererkennung gewährleistet;
10. Erweiterung des Durchmessers: Die gesamte Länge des unterpulvergeschweißten Stahlrohrs mit gerader Naht wird aufgeweitet, um die Maßgenauigkeit des Stahlrohrs zu verbessern und die Spannungsverteilung innerhalb des Stahlrohrs zu optimieren;
11. Hydraulische Druckprüfung: Die expandierten Stahlrohre werden einzeln auf einer hydraulischen Druckprüfmaschine geprüft, um sicherzustellen, dass die Stahlrohre den von der Norm geforderten Prüfdruck erfüllen. Die Maschine verfügt über automatische Aufzeichnungs- und Speicherfunktionen;
12. Anfasen: Bearbeiten Sie das Rohrende des Stahlrohrs, das die Inspektion bestanden hat, um die erforderliche Fasengröße des Rohrendes zu erreichen;
13. Ultraschallprüfung II: Erneute Ultraschallprüfung zur Überprüfung von Fehlern, die nach der Durchmessererweiterung und dem hydraulischen Druck der geradnahtgeschweißten Stahlrohre auftreten können;
14. Röntgeninspektion II: Röntgeninspektion mit industriellem Fernsehen und Fotografie der Rohrschweißnaht am Stahlrohr nach der Durchmessererweiterung und der hydraulischen Druckprüfung;
15. Magnetpulverprüfung von Rohrenden: Diese Prüfung wird durchgeführt, um Defekte an den Rohrenden zu erkennen;
16. Anti-Korrosion und Beschichtung: Qualifizierte Stahlrohre werden entsprechend den Anforderungen der Benutzer korrosionsgeschützt und beschichtet.
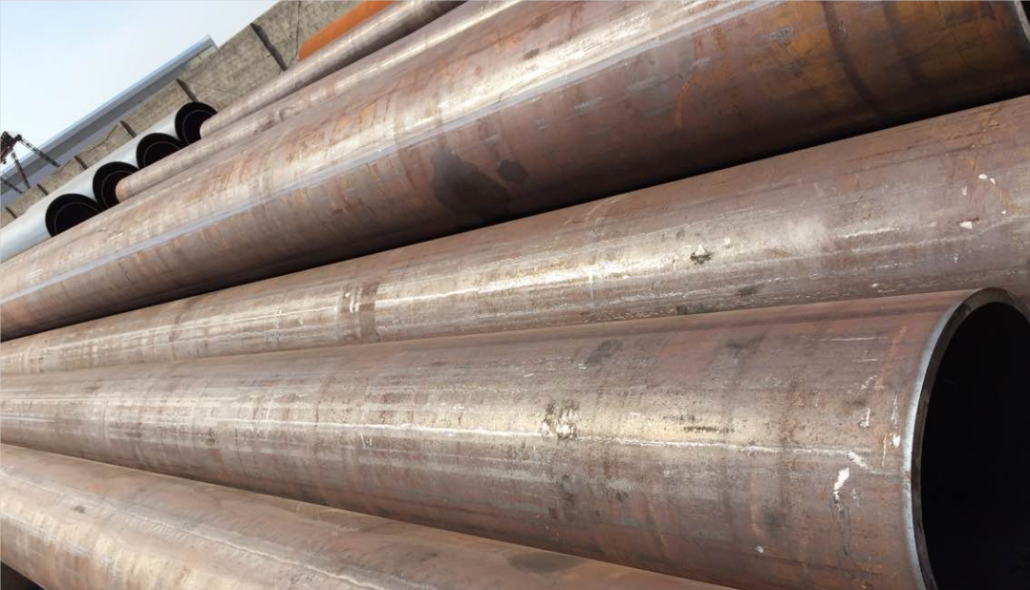
Hinterlasse einen Kommentar
An der Diskussion beteiligen?Hinterlasse uns deinen Kommentar!