Characteristics And Inspection Of Internal And External Plastic-coated Steel Pipes
Internal and external plastic-coated steel pipes for water supply have the following characteristics:
First, the inner surface of the internal and external plastic-coated steel pipe has a plastic coating, which can keep the inside of the pipe smooth, reduce the resistance to water flow, and increase the flow of water. In addition, because the water volume is relatively smooth, the water flow needs can be ensured. At the same time, no scaling will occur inside the pipeline during use, and bacteria will not breed, reducing water pollution.
Second, the outer surface of the internal and external plastic-coated steel pipes has a plastic coating, which can increase the adaptability of the plastic-coated steel pipes. The coating on the outer surface of the steel pipe improves the corrosion resistance, strong water resistance, high oxidation resistance, and good solvent resistance. In addition, the environmental impact on plastic-coated steel pipes can be reduced. Because pipes must be buried underground when supplying water, adding an outer coating can effectively extend the service life of the pipes.
What are the procedures for inspecting plastic-coated steel pipes:
The main inspection methods for plastic-coated steel pipes include appearance inspection, appearance inspection, pinhole test, bending test, flattening test, low temperature test, etc. Each inspection method has its own focus.
Appearance inspection is to inspect the appearance quality of coated steel pipes with the naked eye.
Thickness measurement is to measure the coating thickness at any four orthogonal points on the circumference on any two cross-sections.
The pinhole test refers to using an electric spark leak detector to check the steel pipe coating at the specified test voltage, and also to check whether there is any electric spark.
Bending tests are usually performed on a pipe bending machine or mold. It is worth noting that there is no filler in the pipe during the bending test, and the weld is located on the side of the main bending surface.
The flattening test is to place the specimen between two flat plates and gradually compress it on the pressure testing machine until the distance between the two flat plates is four-fifths of the outer diameter of the specimen. During flattening, the weld of the coated steel pipe is perpendicular to the direction of load application. .
The low-temperature experiment refers to placing the test piece in a low-temperature box, staying there for one hour, and then placing it in a normal temperature environment.
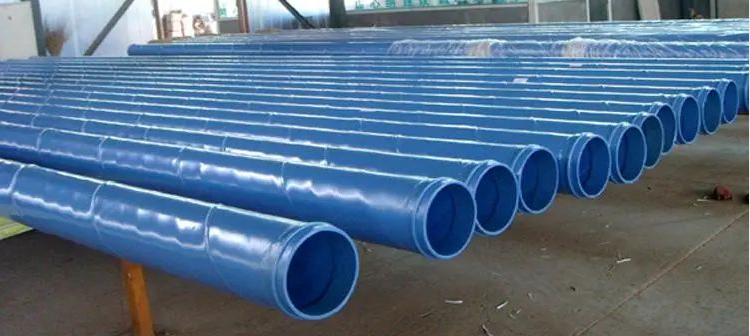
Leave a Reply
Want to join the discussion?Feel free to contribute!