How To Make 3PE Coating Steel Pipes
3PE Coating standard are ANSI/AWWA C104/A21.4 American National Standard for Cement-Mortar Lining for Ductile-Iron Pipe and Fittings for Water, ISO 21809 Petroleum and natural gas industries — External coatings for buried or submerged pipelines used in pipeline transportation systems, DIN 30670 Polyethylen coatings of steel pipes and fittings.
The normal bare pipe will be corroded in the severe environment and its lifetime will be reduced, making the construction and maintenance cost very high. But due to every layer of the 3PE coating system has its good performance, the 3PE coated pipe can protect the pipe in the severe environment and extend its lifetime to 30-50 years even longer. it can significantly reduces the construction and maintainance cost for the pipeline. At the same time, the 3PE coated pipe has favorable thermal insulation property, the thermal losses is just 25% of the traditional pipe, saving a lot of energy cost during operation. At last, the 3PE coated pipe can directly be laid underground or in the water even directly in the frozen earth because of its good anticorrosion property and impact resistance property in the low temperature, no need to construct ditch.
3PE Coating Steel Pipe has good thermal insulation performance, and the heat loss is only 25% of that of traditional pipes. Long-term operation can save a large amount of resources, significantly reduce energy costs, and has strong waterproof and corrosion resistance. With a pipe trench, it can be directly buried in the ground or water. The construction is simple and quick, the overall cost is low, and it has good corrosion resistance and impact resistance under low temperature conditions, and can be directly buried in frozen soil in a certain environment.
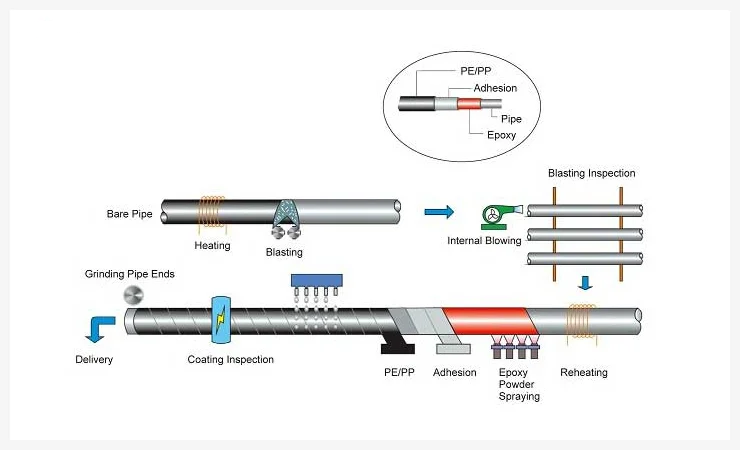