Heat Treatment Defects Of Steel Pipes And Their Prevention
During the heat treatment process of steel pipes, various defects may occur due to improper process parameters, equipment failures, or operational errors. The following is a detailed analysis of common defects and their preventive measures:
I. Defects in the Heating Stage
- Oxidation and Decarburization
Defect manifestation: An oxide scale (Fe₃O₄, Fe₂O₃) forms on the surface of the steel pipe, and the loss of carbon elements leads to a decrease in surface hardness.
Cause: Excessive air (oxidizing atmospheres such as O₂, H₂O, etc.) in the heating furnace, too high a heating temperature, or too long a holding time.
Preventive measures:
Use a controlled atmosphere furnace (such as N₂, Ar protective gas, or drip methanol and acetone to generate a protective atmosphere).
Coat the surface of the workpiece with an anti-oxidation coating (such as a borax coating).
Strictly control the heating temperature and time to avoid overheating. - Coarse Grain (Overheating)
Defect manifestation: The austenite grains grow excessively, resulting in a decrease in mechanical properties (reduction in toughness and plasticity).
Cause: The heating temperature exceeds the critical temperature by a large margin (for example, overheating occurs when the quenching heating temperature is 50~80℃ higher than the Ac3 line), or the holding time is too long.
Preventive measures:
Accurately set the heating temperature (according to the process specifications of the steel grade, for example, the quenching temperature of 45 steel is 840±10℃).
Adopt stepwise heating or rapid heating technology to reduce the residence time at high temperatures.
For overheated workpieces, they can be reprocessed through normalizing (to refine the grains).
II. Defects in the Cooling Stage
- Quenching Cracks
Defect manifestation: Transgranular cracks appear on the surface or inside of the workpiece, mostly occurring at the sudden change of the cross-section, sharp corners, or holes.
Cause:
The cooling rate is too fast (for example, when carbon steel is cooled below the Ms point, the martensitic transformation generates huge internal stress).
The workpiece design is unreasonable (in stress concentration areas), it is not preheated, or there is machining stress before quenching.
The cooling medium is not properly selected (for example, alloy steel is prone to cracking when quenched in brine).
Preventive measures:
Improve the structure of the workpiece (round off sharp corners, avoid large differences in thickness), and carry out stress-relieving annealing before quenching.
Adopt isothermal quenching (bainitic transformation) or step quenching (first quench into a medium above the Ms point and hold it, then cool it slowly).
Select an appropriate cooling medium (for example, 40Cr steel should be cooled in oil instead of water), and control the temperature of the quenching medium (for example, the oil temperature should not be lower than 40℃). - Insufficient or Uneven Hardness
Defect manifestation: The surface or core hardness does not reach the standard, or the hardness difference in the same cross-section is >5HRC.
Cause:
Insufficient heating temperature (incomplete austenitization), insufficient holding time.
Insufficient cooling rate (for example, the aging of the quenching medium and a large amount of impurities lead to a decrease in the cooling capacity).
Surface decarburization (resulting in a lower hardness after quenching).
Preventive measures:
Strictly calibrate the temperature control instrument to ensure uniform heating temperature (the furnace temperature uniformity is ≤±5℃).
Regularly replace or filter the quenching medium (for example, when the water content in the oil is >5%, the water needs to be removed).
Control decarburization (the same as the oxidation prevention measures), and perform surface carburizing compensation if necessary.
III. Defects in the Tempering Stage
- Tempering Brittleness
Defect manifestation: The toughness decreases after low-temperature tempering (200~300℃) (the first type of tempering brittleness), or brittleness occurs during slow cooling after high-temperature tempering (450~650℃) (the second type of tempering brittleness).
Cause:
The first type: Carbides precipitate along the grain boundaries during the decomposition of martensite, which is irreversible.
The second type: Impurity elements such as P and Sn segregate at the grain boundaries, which is reversible (reheating and rapid cooling can eliminate it).
Preventive measures:
Avoid tempering in the brittle temperature range, or use rapid tempering cooling (for the second type of brittleness).
Select steel grades with low impurities, or add alloying elements such as Mo and W to inhibit grain boundary segregation. - Abnormal Hardness after Tempering
Defect manifestation: The hardness after tempering is higher or lower than expected (for example, insufficient hardness after high-temperature tempering after quenching, or higher hardness after low-temperature tempering).
Cause: Incorrect setting of the tempering temperature (for example, mistakenly setting 500℃ as 400℃), failure of the temperature control system, or insufficient holding time.
Preventive measures:
Calibrate the thermocouple and temperature control instrument before tempering (with an accuracy of ±1% FS), and use a dual-sensor monitoring system.
Hold according to the process requirements (generally 1~2 hours, adjusted according to the cross-sectional thickness).
IV. Overall Defects: Deformation and Dimension Out-of-Tolerance
Defect manifestation: The steel pipe is bent, the ovality exceeds the standard (for example, the diameter tolerance is >±0.5%), and the straightness is >1mm/m.
Cause:
The self-weight of the workpiece or improper support during the heat treatment process (for example, a long steel pipe sags when heated while hanging).
There is a large temperature difference in the cross-section during cooling (for example, the cooling rates of the upper and lower surfaces are uneven during horizontal quenching).
Residual stress is not eliminated (for example, direct quenching of a cold-rolled pipe without annealing leads to stress superposition).
Preventive measures:
Use a vertical furnace to heat long steel pipes, or use supporting fixtures to keep them horizontal.
During quenching, rotate or swing the workpiece to ensure uniform cooling (for example, arrange annular nozzles during spray quenching).
Carry out annealing or normalizing before heat treatment to eliminate machining stress, and straighten the finished product (such as pressure straightening or tension straightening).
V. Preventive Management System
- Process Standardization: Develop a “Steel Pipe Heat Treatment Process Card”, clearly defining parameters such as temperature, time, and medium (for example, the normalizing temperature of Q345B steel pipe is 880~920℃, and the holding time is 1min/mm).
- Equipment Maintenance: Regularly calibrate the temperature control system (check once a week), clean the carbon deposits in the furnace (once a month), and check the stirring device of the quenching tank (ensure the flow rate ≥0.5m/s).
- Process Monitoring: Use an infrared thermometer to monitor the surface temperature of the workpiece in real time, and randomly inspect the hardness (at least 3 points per pipe) and metallographic structure (for example, the martensite grade ≤3) for each batch.
- Personnel Training: Operators must work with a certificate and master the heat treatment characteristics of different steel grades (for example, stainless steel solution treatment requires rapid water cooling to avoid the precipitation of the σ phase).
The core preventive idea for heat treatment defects of steel pipes is to precisely control the parameters of the three stages of heating, cooling, and tempering, and reduce stress concentration and organizational inhomogeneity. Through process optimization, equipment maintenance, and process monitoring, the defect rate can be effectively reduced, and the stability of the mechanical properties of steel pipes can be improved.
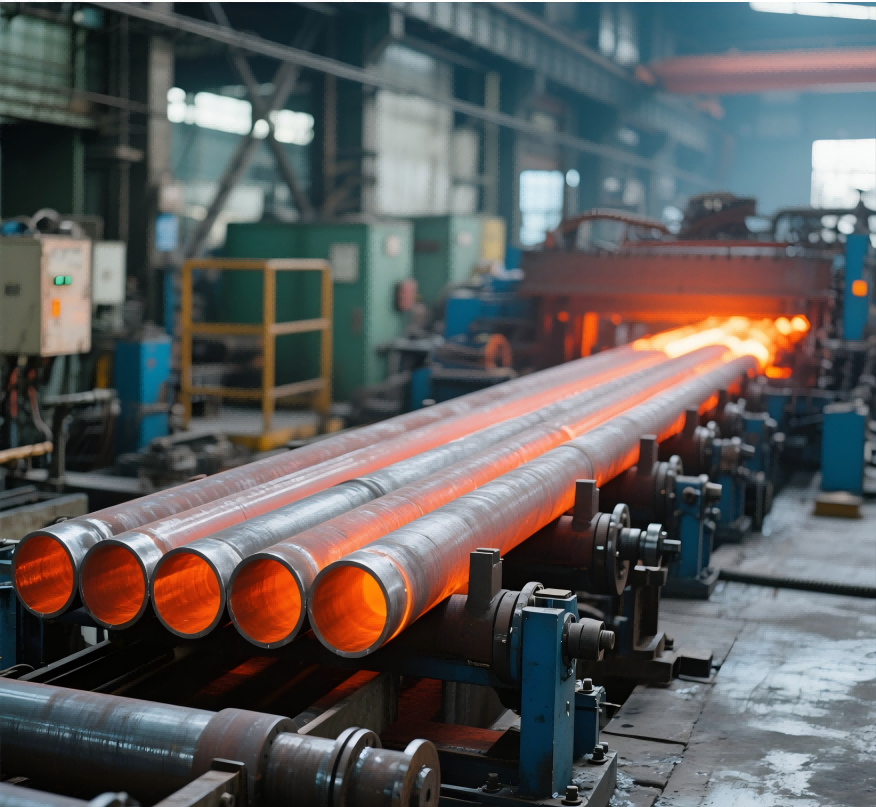
اترك رداً
تريد المشاركة في هذا النقاششارك إن أردت
Feel free to contribute!