Cutting Methods For Anti-corrosion Steel Pipes
There are mainly the following cutting methods for anti-corrosion steel pipes:
Mechanical cutting
External installation cutting: Using the principle similar to that of a lathe, the cutting equipment is installed on the outside of the steel pipe, and the pipe mouth is cut and beveled by a turning tool. This method has a large span for a single machine, a wide range of steel pipe thicknesses that can be processed, less waste, basically no pollution, and no high temperature during processing, so it will not affect the pipe material, which is beneficial to subsequent welding work. It is often used for cutting large-diameter anti-corrosion steel pipes, such as in the construction of long-distance oil and natural gas pipelines, when cutting and cutting 3PE anti-corrosion steel pipes with larger diameters.
Internal installation cutting: The cutting tool is placed inside the steel pipe for cutting operations, which is also based on the principle of turning tool processing. It is suitable for some occasions where it is not convenient to cut from the outside, or where there are special requirements for the cutting quality of the internal steel pipe, such as after the construction of the internal anti-corrosion layer of some chemical pipelines, precise cutting is required inside to meet the process requirements.
Flame cutting
Oxygen-acetylene flame cutting: By adjusting the oxygen valve and acetylene valve, changing the mixing ratio of oxygen and acetylene, three different flames can be obtained: neutral flame, oxidizing flame and carburizing flame. Neutral flame is suitable for cutting general carbon steel anti-corrosion steel pipes; oxidizing flame has a higher temperature and can be used to cut some thicker steel pipes, but it may increase the degree of metal oxidation at the cut; carburizing flame is suitable for cutting high-carbon steel and other steels that are prone to hardening, which can reduce the hardening phenomenon at the cut. At the construction site, oxygen-acetylene flame cutting is a common method for cutting ordinary anti-corrosion steel pipes used for fire protection pipelines.
Plasma cutting: With different working gases, it can cut various metals that are difficult to cut with oxygen cutting, especially for non-ferrous metals such as stainless steel, aluminum, copper, titanium, nickel, etc., and the cutting effect is better. When cutting metals with small thickness, plasma cutting speed is fast. For example, when cutting ordinary carbon steel thin plates, the speed can reach 5-6 times that of oxygen cutting method. The cutting surface is smooth, the thermal deformation is small, and the heat affected zone is also small. Plasma cutting is often used for the processing of some stainless steel anti-corrosion steel pipes that require high cutting accuracy and quality.
Water cutting
High-pressure water is generated by a high-pressure pump, mixed with abrasives such as corundum, and sprayed onto the surface of the steel pipe through a nozzle for cutting. Its incision is clean, the thermal impact on the steel pipe is almost zero, and it will not change the material properties of the steel pipe. The processing span is also large, and it can adapt to the cutting of steel pipes of different diameters. However, the efficiency of water cutting is relatively low, and the processing thickness is limited by factors such as the pressure of the high-pressure pump and the performance of the abrasive. It is generally suitable for the cutting of anti-corrosion steel pipes with high cutting accuracy requirements, strict requirements on material properties, and small cutting volume, such as in the installation of anti-corrosion pipelines in some precision instrument production workshops.
Sawing
Metal saw cutting: General anti-corrosion steel pipes can be cut with metal saws, and small-diameter pipes can be cut with manual or electric metal saws. They are easy to operate, low cost, and can meet general cutting accuracy requirements. For example, in small-scale building decoration projects, manual metal saws can be used to complete a small amount of cutting of anti-corrosion steel pipes below DN50.
Sawing machine cutting: Large diameter pipes should be cut by sawing machine, which has high cutting accuracy, relatively flat cutting surface, and can ensure that the cross section of the pipe is perpendicular to the axis of the pipe. In pipe processing factories, sawing machines are often used when cutting batches of large diameter epoxy resin powder anti-corrosion steel pipes.
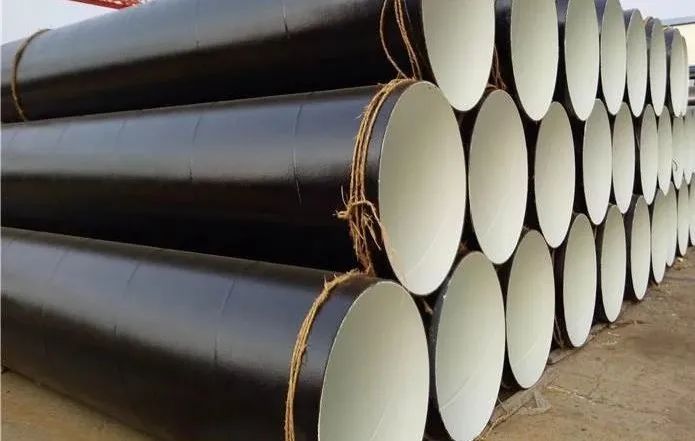
Leave a Reply
Want to join the discussion?Feel free to contribute!